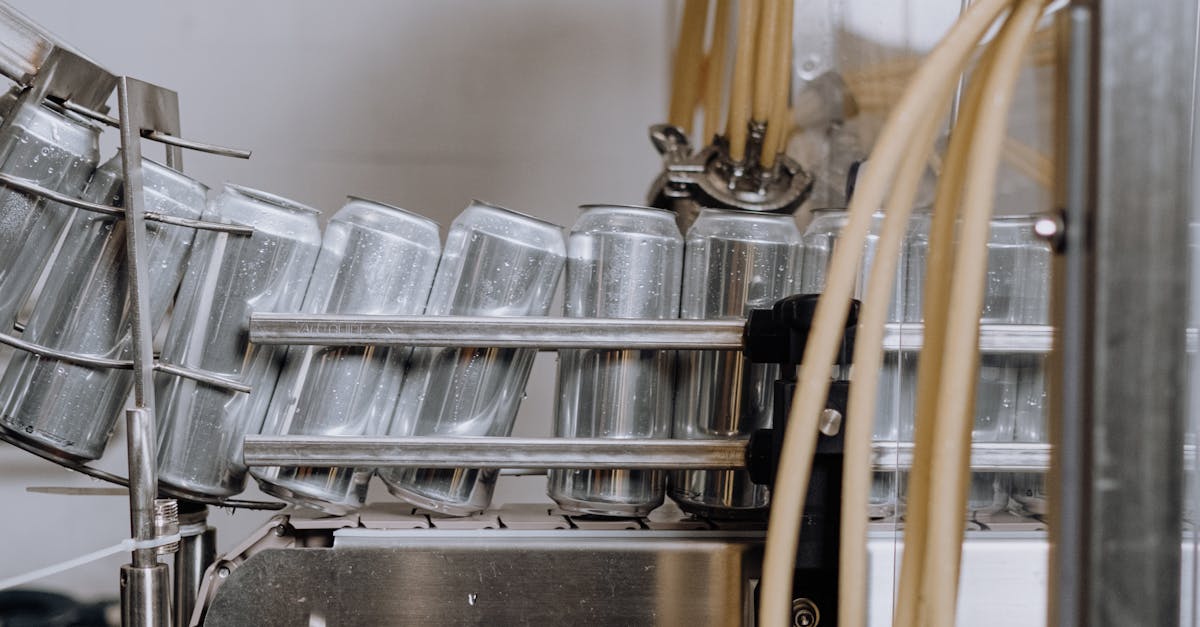
Table Of Contents
Optimising Resource Allocation
Optimising resource allocation is a critical aspect of enhancing operational efficiency within businesses. Through the implementation of advanced technologies, organisations can streamline their resource management processes. Utilising automated systems helps in identifying areas where resources are underutilised or overallocated, enabling businesses to reallocate them effectively. By embracing Business Process Automation near me, companies can ensure that every resource is optimally utilised to achieve maximum productivity and cost-effectiveness.
Moreover, with the aid of automated tools, businesses can gain real-time insights into resource allocation patterns and trends. This allows for swift adjustments to be made in allocation strategies, ensuring that resources are directed to where they are most needed. By integrating automated solutions into resource allocation processes, businesses can not only enhance their operational performance but also better align their resources with their strategic objectives.
Implementing Automated Task Assignments
Implementing automated task assignments is a strategic move for businesses aiming to streamline their operations. By incorporating automated systems into the assignment process, organisations can achieve greater efficiency and productivity in task allocation. With the help of task assignment automation, businesses can accurately assign tasks to individuals based on their skills and availability, ensuring optimal resource utilisation. This can lead to a more effective use of resources and improved time management, ultimately driving increased performance and output. Business Process Automation near me becomes essential in leveraging the benefits of automated task assignments for enhanced operational effectiveness and productivity growth.
For businesses looking to enhance their task management processes, automated task assignments offer a range of advantages. These automated systems can help minimise delays in task allocation, ensuring that deadlines are met promptly. Furthermore, by automating the task assignment process, organisations can reduce the risk of errors associated with manual task allocation. This not only enhances the overall accuracy of task assignments but also contributes to improved quality control measures. Embracing Business Process Automation near me can significantly enhance the task assignment process, resulting in more streamlined operations and improved organisational performance.
Increasing Efficiency
When it comes to enhancing operational efficiency, Business Process Automation near me emerges as a game-changer. One example of this is the automation of inventory management processes. By implementing automated inventory management systems, businesses can significantly reduce the time and effort required to track and manage stock levels. This not only streamlines operations but also minimises the risk of overselling or running out of critical items. Through the use of advanced algorithms and real-time data, businesses can ensure optimal stock levels and effectively meet customer demands.
Another pivotal aspect of increasing efficiency through Business Process Automation near me is the implementation of automated quality control systems. By automating quality control processes, businesses can enhance product consistency and reduce the likelihood of defects slipping through the cracks. These automated systems can swiftly detect abnormalities or deviations in product specifications, allowing for immediate corrective actions to be taken. This not only saves time and resources but also upholds the reputation of the business by delivering high-quality products consistently.
Automating Inventory Management Processes
Automating inventory management processes is crucial for businesses seeking to streamline their operations and improve overall efficiency. Utilising advanced software and technology, companies can accurately track their inventory levels, monitor stock movements, and generate real-time reports to inform decision-making. By implementing automated inventory management systems, organisations can reduce manual errors and save valuable time that can be directed towards other strategic initiatives. For businesses looking to enhance their inventory control mechanisms, exploring options for Business Process Automation near me could offer tangible benefits in terms of cost savings and operational effectiveness.
Furthermore, automating inventory management processes can help businesses prevent stockouts, identify trends in product demand, and optimise their supply chain operations. By integrating automated inventory solutions into their business processes, companies can improve order fulfilment rates and enhance customer satisfaction levels. Embracing technology for inventory management not only leads to accuracy and efficiency but also frees up employees from mundane tasks, allowing them to focus on more value-adding activities. For those interested in upgrading their inventory management practices, seeking opportunities for Business Process Automation near me could be a strategic move to stay competitive in today's dynamic marketplace.
Reducing Human Errors
To reduce human errors, businesses can adopt Business Process Automation near me solutions that streamline operations and minimise manual intervention. By implementing automated workflows and checks, organisations can decrease the likelihood of mistakes occurring in routine tasks. For instance, automation tools can help in processing transactions accurately and efficiently, ensuring data accuracy and compliance with regulations.
Moreover, utilising automated quality control systems can play a pivotal role in enhancing the accuracy levels throughout the production process. These systems can conduct thorough inspections and flag any deviations from the specified standards promptly. By incorporating such technologies into their operations, businesses can elevate their efficiency and deliver high-quality products or services consistently.
Implementing Automated Quality Control Systems
Implementing Automated Quality Control Systems streamlines production processes, ensuring consistency and accuracy in the final product. By integrating sensors and monitoring devices into the manufacturing line, businesses can detect defects promptly and make real-time adjustments. This not only enhances product quality but also minimises the potential for costly recalls and rework, ultimately boosting customer satisfaction.
Business Process Automation near me can revolutionise quality control by automating inspection tasks and identifying deviations from set standards without human intervention. This reduces the reliance on manual checks, which are prone to oversight and fatigue-induced errors. Automated quality control systems can operate 24/7, providing continuous monitoring to uphold quality levels consistently and efficiently.
FAQS
What is process automation?
Process automation is the use of technology to streamline and automate repetitive tasks and processes within an organization.
How can process automation help in optimising resource allocation?
Process automation can help in optimizing resource allocation by efficiently assigning tasks based on availability, skills, and workload, leading to better utilization of resources.
What are some examples of implementing automated task assignments?
Examples of implementing automated task assignments include using workflow management tools to assign tasks based on predefined rules, deadlines, and priorities.
How does process automation increase efficiency in operations?
Process automation increases efficiency by reducing manual interventions, minimizing delays, and improving the speed and accuracy of tasks and processes.
Can you provide examples of automating inventory management processes?
Examples of automating inventory management processes include using barcode scanning systems, RFID technology, and inventory management software to track and manage stock levels automatically.
How does process automation help in reducing human errors?
Process automation reduces human errors by eliminating manual data entry, automating repetitive tasks prone to errors, and implementing validation checks and automated alerts.
What are some examples of implementing automated quality control systems?
Examples of implementing automated quality control systems include using sensors and monitoring devices to detect defects, automated testing procedures, and real-time data analysis to ensure product quality.